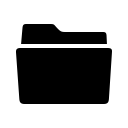
Uncategorised (4996)
Snake-arm robot showcased at offshore inspection capabilities at ITF event
AdministratorDelegates at ITF Technology Showcase were given an insight into how a novel snake-arm robot could take offshore inspection to a new level ahead of its first trial with Chevron.
Technology developer, OC Robotics has proven the capability of the P100 snake-arm robotic inspection system onshore and is now exploring the feasibility of robotic inspection of offshore oil and gas pressure vessels. Snake-arm robots are driven by wire ropes and controlled by OC Robotics’ proprietary software. Snake-arm robots are especially suited to working in confined and hazardous spaces as they can navigate and traverse cluttered environments. Only the arm itself is deployed into the workspace as the main drive motors, electronics and control systems are located away from the inspection area.
The project is being funded by Innovate UK’s ‘Energy Game Changer’ programme. OC Robotics & Chevron are exhibiting on Innovate UK’s stand along with a number of companies that secured funding through the competition last year. Innovate is the UK’s innovation agency which aims to drive science and technology innovations that will grow the UK economy - delivering productivity, new jobs and exports.
As part of the project, a world first offshore trial will take place on one of Chevron’s North Sea assets to assess current capabilities and future needs for long-term operation of robotic equipment. OC Robotics is adapting its existing technology to be more robust and adaptable for the restricted access encountered on offshore rigs, such as deck layouts, narrow walkways and handrails.
Russell Brown, Senior Reliability Engineer, Chevron ETC said: “We inspect our assets at regular intervals to determine their continued fitness for service and prevent asset-integrity or process-safety-related incidents. This causes a dilemma as, to do so, we have to perform high-risk, confined-space inspections. To this end, Chevron and the wider industry have been looking for solutions that will help minimise human entry in confined and hazardous environments for tasks like cleaning and inspection.”
Rebecca Smith, Project Manager at OC Robotics said: “Our project is innovative in the deployment of robotic technology in harsh environments, such as the North Sea. There is real potential to improve inspection outputs and extend asset life by characterising vessels and assessing fitness for service without human entry into dangerous and confined spaces. We are at an exciting stage with the P100 and we look forward to telling our story to a like-minded audience at the Showcase.”
The annual ITF Technology Showcase at AECC – Technology in Action - brings together some of the brightest minds from inside and outside of oil and gas to challenge current thinking and bring fresh focus on progressing new solutions.
Dr Geoff McGrath, Chief Innovation Officer at McLaren Applied Technologies and the KPMG McLaren Alliance will give a keynote on ‘innovation from outside our industry’ at the conference and exhibition at AECC on Wednesday 1st March.
Other plenary speakers include Colette Cohen, Chief Executive of the Oil & Gas Technology Centre (OGTC), Dr Geoff Nesbitt, Group Head of Technology Strategy at Petrofac and Willie Reid, Director of the Strathclyde Oil and Gas Institute. Gunther Newcombe, Director of Operations, Oil and Gas Authority (OGA) and Greta Lydecker, Managing Director, Chevron Upstream Europe will also join the morning panel session.
An Innovation hall will be dedicated to supporting the innovator community and showcasing the very best in new thinking, products, solutions and services.
The technology sessions are facilitated by oil and gas operators with a keen interest on getting technology to market through the most effective and efficient routes possible. The three sessions this year will focus on:
- Applied Digital Technologies to Improve Operational Efficiency and Performance
- Transformational manufacturing and new materials to reduce costs
- Emerging Inspection and Condition Monitoring Technologies to Prevent Failure in Operation and Avoid Downtime
Baumüller is once again investing in the field of contract manufacturing of electronic assemblies and systems
EMS services (Electronic Manufacturing Services) cover the entire range of contract manufacturing of electronic assemblies, devices and systems. In addition, EMS is a method of outsourcing where parts of the value added chain are outsourced to a partner in order to optimize costs and to be able to concentrate more on the development of new products, marketing and sales.
As a competent partner in the field of contract manufacturing, the drive and automatization specialist Baumüller based in Nuremberg supports its customers across the entire value added chain: from consultation to prototype production to series production. Baumüller continuously invests in this sector in order to expand its production of electronic assemblies.
Baumüller continues to invest in the latest production technology. The new selective soldering system increases efficiency and process safety
With the new ERSA Smartflow, Baumüller is offering its customers an economically and qualitatively attractive alternative to the manual and wave soldering process. This is the perfect solution, especially when layouts of products are frequently changed or only small quantities of a certain type are to be produced. The new selective soldering system has features that ensure process safety, such as the spray jet monitoring or process monitoring cameras. The Ersa SMARTFLOW was specifically developed for difficult soldering processes in order to replace manual soldering here as well. This ensures the highest level of precision in selective soldering technology and allows for a faster processing of these soldering operations.
A real win for contract manufacturing: All process parameters are stored in a database, which can be quickly accessed if a new order is issued or in the event of inquiries.
New contact partner for EMS services
The field of EMS services at Baumüller has a new contact partner. Dominik Brendel has several years of experience in the field of EMS and joined the Baumüller Group at the end of 2016. As the manager for the EMS area, Mr. Brendel joins as the successor to Herbert Kutsche, who is retiring after a long and successful career at the company and who in the future will act as an advisor for Baumüller.
More information about the Baumüller EMS services can be found at https://www.baumueller.de/
About Baumüller Gruppe
Baumüller is one of the leading manufacturers of innovative automation and electric drive systems. At six manufacturing locations and over 40 subsidiaries spread all over the world, 1700 employees plan, develop, produce and install intelligent system solutions for mechanical engineering; from operation and visualization tools to Motion Control software as per PLCopen, from software modules to controllers, also including converters, electric drives and the whole service range for ready to use automation solutions.
The areas service, installations, fitting, and relocation add to the wide range of Baumüller's services. In the mechanical engineering industry, Baumüller is one of the leading partners for automation solutions worldwide.
Inauguration at Valmet delivered biomass based power plant in Skövde in Sweden
AdministratorThe inauguration of Skövde Värmeverk`s new Valmet delivered biomass based power plant was held on Wednesday March 22nd, 2017. The inauguration speech was kept by Minister for Policy Coordination and Energy Ibrahim Baylan. Other speakers in the inauguration were Sammy Tanhua, CEO of Skövde Värmeverk, chairman of the board, Philip Segell and municipal counsellor Leif Walterum. The official inauguration was followed by a tour at the power plant.
Minister for Policy Coordination and Energy Ibrahim Baylan kept the inauguration speech
"It's a great day for us as a company and for the municipal of Skövde. With this additional biomass plant we will be able to deliver sustainable and climate neutral heating and power to Skövde and also be prepared for future growth of the city. This new plant will help to reduce 40 000 tonnes of CO2 emissions on annual basis. The project has run smoothly and we are very pleased in the project organization with Valmet as the lead contractor," says Sammy Tanhua, CEO of Skövde Värmeverk AB.
"It has been a great pleasure to follow the project from the first contacts to this inauguration. And it is satisfying to see the proud customer showing the inauguration guests this very nice plant," says Mikael Barkar, Senior Sales Manager, Energy Sales and Services Operations, Valmet.
Technical information about the power plant
The new power plant produces district heat to the local district heat network and electricity to the national grid. The boiler is fueled with wood chips and bark. The power plant has a thermal capacity of 38 MWth and additional 8.5 MWth is recovered from water vapor using Valmet's flue gas condensing technology.
Valmet's complete process delivery from fuel reception to stack included a biomass-fired HYBEX boiler, a flue gas condensing scrubber, a combustion air moisturizing tower, CO2 and NH3 scrubbers, condensate treatment, electrification, instrumentation and automation.
Skövde Värmeverk`s new biomass based power plant
Information about Skövde Värmeverk
Skövde Värmeverk is a limited liability company owned by Skövde municipality and was established in 2003. The company's task is to produce environmentally friendly electricity and district heating in Skövde municipality.
Valmet is the leading global developer and supplier of process technologies, automation and services for the pulp, paper and energy industries. We aim to become the global champion in serving our customers.
Valmet's strong technology offering includes pulp mills, tissue, board and paper production lines, as well as power plants for bioenergy production. Our advanced services and automation solutions improve the reliability and performance of our customers' processes and enhance the effective utilization of raw materials and energy.
Valmet's net sales in 2016 were approximately EUR 2.9 billion. Our 12,000 professionals around the world work close to our customers and are committed to moving our customers' performance forward - every day. Valmet's head office is in Espoo, Finland and its shares are listed on the Nasdaq Helsinki.
‘Green Gas is a fundamental part of the energy trilemma solution’ says the Energy and Utilities Alliance, EUA’s CEO Mike Foster on the release of an informative video showcasing Green Gas.
Mr Foster continued;
Gas has for the past two hundred years been a fuel that has offered the UK flexibility – be it for street lighting; industrial processes; power generation or heat demand. As a result of its abundance, the UK has the world’s leading gas grid infrastructure in place, directly supplying the energy to heat 85 per cent of UK homes.
Rather than rip out heating systems and make the grid obsolete, it makes sense to decarbonise the gas we use; using so called green gases such as Biomethane and bio-SNG in addition to hydrogen, will deliver affordable and sustainable solutions to the challenges the UK face. Green gas is increasingly being recognised as the preferred solution to meet UK heat demand, which is seasonal and demands a flexible supply.
Green Gas is the logical solution to the decarbonisation of heat in the UK. In 2016 Green Gas production doubled and so the focus now is really on progressing the production of Green Gas, rather than ‘what if’.
The short video we are releasing today is the next stage of the process- increase awareness. The industry has proven the concept, it’s now time to educate others on the future of UK heat.’
A new report has just been launched by the Centre for Alternative Technology (CAT) explores the barriers to reaching net zero greenhouse gas emissions, looking at how these can be overcome in a way that could bring a wide range of additional benefits.
‘Zero Carbon Britain: Making it Happen’ brings together a broad range of evidence from academic literature and grassroots projects to create a picture of the inter-related solutions that we need to reach zero carbon.
Rather than an unresolved technical challenge, it is increasingly accepted that rising to the climate challenge presents a mix of psychological, political and economic barriers. Zero Carbon Britain: Making it Happen sets out the positive, connected approach we need to overcome them.
Mapping out cutting-edge solutions from psychology, sociology, political science, economics and other social sciences, the report also draws on lessons from arts, culture, and faith and spiritual practice. Drawing on findings from a wide range of peer-reviewed research, it integrates these with leading expert views and stories from real-life projects that demonstrate how we can overcome barriers in innovative and exciting ways.
Project Coordinator Paul Allen said: “Providing clear evidence that workable solutions already exist is vital. It empowers citizens and gives policymakers no excuse for inaction. CAT’s previous research has shown that we have all the tools and technologies we need; this new report now demonstrates how we can overcome the cultural, economic and political barriers.”
CAT Chief Executive Adrian Ramsay said: “The shift to zero carbon could be one of the most exciting opportunities in human history, offering many benefits including better housing, accessible transport, reduced obesity, better physical and psychological wellbeing, and more jobs. It’s essential that we understand and start to overcome the barriers to making this shift happen.”
This year’s SWANApalooza conference and exhibition opens in Reno, Nevada today March 27th. The four-day event will feature the 40th annual landfill gas and biogas symposium and 21st annual landfill symposium as well as technical sessions covering the prominent topics of the solid waste industry.
Sulzer will once again attend the SWANA Symposium and present a number of innovative solutions designed to improve the reliability and efficiency of engines powered by landfill gases.
Landfill gas is commonly used to fuel engines that power generators to produce electricity, but the variable methane content means this useful by-product needs to be carefully managed. Without precise control mechanisms, the efficiency of the combustion process may be compromised, which will have a knock-on effect on emissions.
Sulzer has developed an innovative turnkey solution that can be used in conjunction with your existing engine control system to improve engine performance and reliability.
The latest solution from Sulzer uses advanced engine performance controllers, sensors and catalysts to create a bespoke package that can be installed alongside the existing engine controls, improving engine performance and reliability. Precision engine control is delivered by an advanced management system and combined with the latest catalysts to reduce emissions and improve efficiency.
Sulzer is a leading OEM pump manufacturer and independent service provider for all brands of rotating equipment including pumps, generators and electric motors, turbines and compressors. With a worldwide network of service centers, Sulzer has the facilities and expertise to deliver turnkey solutions anywhere in the world.
For more information or to discuss a specific application, visit the Sulzer staff at booth 618.
About Sulzer:
Sulzer is the leading worldwide, independent service provider for the repair and maintenance of rotating machines including turbomachinery, pumps and electro-mechanical equipment. With a global network of over 150 technically advanced manufacturing and test facilities, Sulzer offers a collaborative advantage that delivers high-quality, cost-effective, customized and turnkey solutions, providing its customers with the peace of mind to focus on their core operations.
Sulzer Rotating Equipment Services, a division of Sulzer, can accommodate all brands of rotating equipment including turbines, compressors, generators, motors and pumps. With an enviable track record, dedicated teams of on-site engineers provide best-in-class solutions to ensure that the most effective service is delivered.
Sulzer is dedicated to providing superior service solutions to a range of industries including power generation, oil and gas, hydrocarbon and chemical processing, water and air separation. Every solution is customized to suit the business needs of each application – whenever or wherever that may be.
With a long history of providing engineering service support, Sulzer is headquartered in Winterthur, Switzerland where it began in 1834. Today, with sales over US$ 3 billion and with approximately 15,000 employees, the Sulzer footprint spans across the globe. The core aim is to deliver a flexible and cost-effective service that optimizes customer operational efficiency and minimizes downtime.
For more information on Sulzer, visit www.sulzer.com
Uptime-as-a-Service leader Senseye launches next generation of predictive maintenance software to include Remaining Useful Life analysis
AdministratorSenseye, the Uptime-as-a-Service leader, has just announced the launch of version 2.3 of its automatic condition monitoring and prognostics software, bringing Remaining Useful Life calculations to all customers – whether they operate 10 or 10,000 assets. Senseye is the only product in the world to offer automated condition monitoring combined with Remaining Useful Life analysis.
Knowing the Remaining Useful Life of machinery helps industrial companies to implement cost-effective predictive maintenance, typically allowing for a 10-40% reduction in maintenance costs and downtime reduction of 30-50%. The software is already trusted by a major automotive OEM, helping them to avoid downtime costs of over $2m per hour.
Remaining Useful Life has been an academic focus until now, accessible only to those with extensive data engineering skills. Senseye’s patent-pending technology makes it accessible to all. Its automated analysis is designed to be easy to use by maintenance teams and managers and is backed by Senseye’s extensive background in condition monitoring from the highly competitive aerospace & defence industry.
Robert Russell, Senseye CTO says, “Being able to see the Remaining Useful Life of machinery – without requiring expert input – empowers the hero maintainers to get maximum value from their condition monitoring solutions.”
Trusted by a number of Fortune 100 companies, Senseye is the leading cloud-based condition monitoring and prognostics product. The award-winning solution is usable from day one and available as a simple subscription service, enabling customers to rapidly expand their predictive maintenance programs.
About Senseye Ltd. Leading Uptime-as-a-Service company Senseye develops cloud-based software that automates condition monitoring and prognostics, enabling subscribers to predict failures in machinery months in advance. Senseye harnesses data science, deep expertise in machine learning and real-world industry know-how to provide a robust and scalable approach to reducing downtime and operational costs. www.senseye.io
TGS and Schlumberger Announce New Multi- and Wide-Azimuth Multiclient Reimaging Program in Central U.S. Gulf of Mexico
AdministratorNew reimaged data covers 1,000 OCS blocks ahead of large regional lease block turnover
TGS-NOPEC Geophysical Company (TGS) and Schlumberger have just announced a new multi- and wide-azimuth (M-WAZ) multiclient reimaging program in the highly prospective Central U.S. Gulf of Mexico. Final results are expected in early 2018, ahead of a period when substantial block turnover in the area is anticipated.
The new Fusion M-WAZ reimaging program comprises data covering more than 1,000 Outer Continental Shelf (OCS) blocks (~23,000 km2) from 3D WAZ programs previously acquired by TGS and Schlumberger with the WesternGeco Q-Marine* point-receiver marine seismic system between 2008 and 2012. This large reimaging program will process data from the Mississippi Canyon, Atwater Valley and Ewing Bank areas using the latest imaging technology to provide a significant uplift in data quality for upcoming licensing rounds. The area is expected to remain a high priority for E&P companies in the foreseeable future and will benefit from two licensing rounds every year for the next five years under the new BOEM 2017-2022 Five-Year Program.
“This highly prospective region is a core area for TGS and Schlumberger, where we have a close relationship with customers who continue to demand the best data to support their exploration and drilling activities,” said Kristian Johansen, CEO, TGS. “We have a strong track record of adding value to existing data sets through reprocessing with the latest technology. Fusion is the largest wide-azimuth reprocessing project ever performed by TGS in our collaboration with Schlumberger.”
Maurice Nessim, president, WesternGeco, Schlumberger, added, “This reimaging collaboration combines the use of the latest reimaging technology with high quality Q-Marine measurements and extensive geophysical and geological knowledge of this prolific area. Customers have shown great interest and we are confident that this project will afford them a competitive advantage in the upcoming lease rounds and ahead of the large block turnover.”
The custom-processing workflow for this project will include a number of newly developed imaging technologies including 3D WAZ de-ghosting; 3D surface related multiple elimination (SRME); common offset RTM gather (COR) and image-guided tomography; and orthorhombic anisotropy velocity modelling. During the reprocessing, geoscientists will update the salt interpretation and add input from the latest well data released for the area.
The reimaging program is supported by industry funding. Fast-track data will be available in 2017 for lease round bid evaluation.
About the Companies
TGS-NOPEC Geophysical Company (TGS) provides multi-client geoscience data to oil and gas Exploration and Production companies worldwide. In addition to extensive global geophysical and geological data libraries that include multi-client seismic data, magnetic and gravity data, digital well logs, production data and directional surveys, TGS also offers advanced processing and imaging services, interpretation products, and data integration solutions.
For more information visit TGS online at www.tgs.com
Schlumberger is the world's leading provider of technology for reservoir characterization, drilling, production, and processing to the oil and gas industry. Working in more than 85 countries and employing approximately 100,000 people who represent over 140 nationalities, Schlumberger supplies the industry's most comprehensive range of products and services, from exploration through production, and integrated pore-to-pipeline solutions that optimize hydrocarbon recovery to deliver reservoir performance.
Schlumberger Limited has principal offices in Paris, Houston, London and The Hague, and reported revenues of $27.81 billion in 2016. For more information, visit www.slb.com
Rotork electro-hydraulic actuators provide increased safety at Mauritius International Airport
AdministratorIn a project to increase safety, Rotork Skilmatic SI electro-hydraulic actuators have been installed in the Joint Users Hydrant Installation (JUHI) fuel storage depot at the Sir Seewoosagur Ramgoolam (SSR) International Airport in Mauritius.
Replacing obsolete electric actuators from another manufacturer, the Profibus-enabled, ATEX-rated failsafe Rotork actuators have been installed in critical valve areas to prevent potential spillages by automatically closing-off the flow of fuel on receipt of an overfill alarm signal.
An Electrical & Control Specialists Ltd. engineer completes the installation of one of the new Rotork Skilmatic SI actuators in the JUHI fuel storage depot at the SSR International Airport in Mauritius.
Skilmatic self-contained actuators have been specifically designed as the reliable solution for this type of vital failsafe application. The actuators combine the simplicity of electrical operation with the precision of hydraulic control and the reliability of mechanical failsafe action, utilising an integral spring mechanism to provide the most reliable means of positioning a valve to a pre-determined safe position. Incorporating an intelligent control and monitoring system as standard, SI actuators provide an ideal solution for two position or safety shutdown duties in Safety Instrumented Systems (SIS) or precise modulating control applications.
In addition to the Profibus DP control, Rotork datalogging and monitoring options provide a valve signature profile and historical record of valve torque demands. Using the Rotork non-intrusive intrinsically safe Bluetooth® setting tool, these configuration and datalogger files can be transferred from the field to a standard PC for analysis as part of the asset management programme.
The actuator installation was performed by Rotork’s South Africa office and their Mauritian agents, local company Electrical & Control Specialists Ltd., whose responsibilities encompassed removing the old actuators and cabling, designing and fabricating new valve adaption, fitting the Rotork actuators, wiring-up and commissioning.
For sixty years, engineers have relied upon Rotork for innovative and dependable flow control solutions. Rotork products and services are helping companies in the oil & gas, water and waste water, power, marine, mining, food, pharmaceutical and chemical industries around the world to improve efficiency, assure safety and protect the environment.
Energy Institute (EI) and the Emirates National Oil Company (ENOC) to host international technical forum on HSE in the Middle East
AdministratorEI and ENOC have signed an agreement to host a joint international technical forum on health, safety and environment in the Middle East to take place in Dubai, 16-18 May 2017.
Bringing together research, academia, industry and regulators, the conference will discuss HSE challenges and opportunities facing the energy sector in the region. It aims to deliver essential learning and sharing of international best practice to help improve the health, safety and environmental performance of organisations, foster a healthy and accident-free work culture, and ensure a sustainable environment.
The forum will include a two-day technical conference, 16-17 May 2017, followed by technical workshops on 18 May. The workshops will examine selected topics in detail while referencing relevant EI technical publications that already capture knowledge, good practice and lessons learned.
Topics to be discussed over the three days include:
- The outlook for the energy sector in the GCC
- The impact of the Paris Agreement on climate change on the oil and gas industry
- Managing health hazards and reducing their impact on workers’ wellbeing
- Demonstrating best practices in assessing and mitigating hazards, particularly around potential major accidents and environmental impacts
- HSE leadership
- Unlocking future talent and inspiring people
Dr Mark Scanlon MEI, EI Head of Good Practice – HSE said: ‘For over 75 years, the EI has produced safety guidance for the energy sector. In today’s world, there are more technologies and complex processes than ever before and the need is ever growing for relevant and up-to-date good practice to ensure the changing energy industry can manage its operations without impacting people, assets and the environment. This event will provide a platform to discuss health, safety, environment and sustainability in a more holistic manner. There will be opportunities for open discussion and, most importantly, the chance to exchange ideas with the international HSE community.’
Louise Kingham OBE FEI, EI Chief Executive added: ‘The EI has a unique role as a learned society to provide a safe place to discuss and seek to solve the challenges that the industry faces. We support people and organisations to make the transitions that are essential for the future, driving up skills and standards and facilitating collaboration for the benefit of all. This agreement with ENOC to host the Middle East HSE Forum fullfills our objective to contribute skills, knowledge and good practice towards a safer and more environmentally-responsible energy system.’
His Excellency Saif Humaid Al Falasi, Group CEO, ENOC, said: “Safety is a key performance indicator of the UAE Vision 2021 National Agenda. As an integrated player across the country’s energy value chain, ENOC is committed to following international best practices in health, safety and environment to ensure the well-being of the communities we serve. We have led the dialogue on energy safety in Dubai with like-minded partners, which resulted in continuously raising the bar of excellence in HSE implementation. Our collaborative efforts with EI will continue that dialogue within the regional energy ecosystem to reinforce safety and security standards for the O&G sector in the Middle East.”
For further information and to register, visit www.energyinst.org/MiddleEast-HSE
The Energy Institute (EI) is the leading chartered professional membership body for the energy industry, supporting over 23,000 individuals working in or studying energy and 200 energy companies worldwide. The EI provides learning and networking opportunities to support professional development, as well as professional recognition and technical and scientific knowledge resources on energy in all its forms and applications. The EI’s purpose is to develop and share knowledge, skills and good practice towards a safe, secure, affordable and sustainable energy system. A registered charity, the EI serves society by offering scientifically sound information on energy issues and a neutral platform for debate. As the only industry-wide professional body, covering all disciplines and forms of energy, the EI has great strength in the diversity and expertise of its members. For more information, please visit www.energyinst.org
About ENOC:
Emirates National Oil Company Group (ENOC) is a leading integrated global oil and gas player operating across the energy sector value chain. A wholly owned company of the Government of Dubai, ENOC Group offers a diverse portfolio of assets operating across five business segments: Supply, Trading and Processing, Terminals, Marketing, Retail and Exploration and Production. Servicing thousands of customers across 60 markets, the Group employs a workforce of over 9,000 employees and is deploying its world-class customer service, latest innovations and technologies and best practices towards the UAE’s social and economic development. For further information, please visit: www.enoc.com
More...
Outstanding abravise wear test results on austenitic stainless steel after SuperExpanite Surface Hardening.
AdministratorAbrasion wear is an extensive problem for stainless steels. In the on-going effort to increase the knowledgebase on abrasion, Expanite requested Bud Labs to measure the dry abrasion characteristics of untreated and Expanite treated samples of austenitic AISI316L using the ASTM G 65 Procedure
Labs to measure the dry abrasion characteristics of untreated and Expanite treated samples of austenitic AISI316L using the ASTM G 65 Procedure.
The ASTM G 65 Procedure is a standard test method for measuring abrasion using the dry sand/rubber wheel apparatus where weight loss is used as indicator for the wear resistance; the less the better.
The results are indisputable: The 316L with SuperExpanite is more abrasion resistant than the untreated sample approximately reducing abrasive wear by more than 60%.
The table below lists the observed weight losses and thereby the reduction on an Expanite hardened sample:
Not just a coating
The Expanite treatment effectively removes the oxide film covering stainless steels. This allows controlled incorporation of carbon and nitrogen atoms in the underlying metal. The hardened layer is characterized by an expansion of the material structure. We call this zone expanded austenite, expanded martensite, or simply, Expanite.
With the Expanite process it’s possible to increase the surface hardness of stainless steels by up to 10 times, while maintaining or even enhancing corrosion resistance. This method is considered unique since it’s suitable for austenitic-, ferritic-, martensitic and duplex stainless steels. Parts can be treated with extremely short lead times—a few days—which is previously unseen within surface hardening of stainless steel.
The Expanite technology can significantly increase the value of products across many industries—from knives, valves, mixers, and grinders for the food industry, to pumps and extruder screws, or injection parts for the automotive sector, as well as screws, bolts, and washers.
At its core, Expanite offers 3 different processes, each of which can be optimized according to customers’ requirements in terms of abrasion, galling, corrosion and scratch resistance. This means that Expanite can develop and customize solutions for a wide variety of companies and industries.
Expanite
Expanite was founded in 2010 by three scientists from The Technical University of Denmark. Expanite is based in Hilleröd, Denmark, has a treatment facility located in Twinsburg, Ohio and Expanite recently opened a treatment center in Frickenhausen, Germany. For further information, please contact Thomas Abel Sandholdt, CEO at Expanite, +45 2040 7207, or check our website: www.expanite.com.
Traypacker chain offers unrivalled benefits to food and beverage industry
AdministratorTsubaki has developed a special chain for the tray packing machinery widely used in the food and beverage industry. It is internally lubricated so that it is clean in use and does not need regular re-lubrication.
Tsubaki Traypacker Chain is a development of the company’s Lambda solution, which uses a special sintered oil-impregnated bush. Like the latest generation of Tsubaki Lambda Lube Free chain, the Traypacker is impregnated with NSF-H1 food grade lubricant as standard.
Tsubaki Traypacker Chain is a development of the company’s Lambda solution, which uses a special sintered oil-impregnated bush.
Tray packing machinery is common in the food and beverage industry and fits cardboard trays or boxes to items, often to create ‘multi-packs’, before distribution. Naturally, hygiene is paramount and standard lubricated chain can cause contamination of the machine, floor and end product, possibly resulting in increased maintenance requirements, damaged products and reduced profit. Furthermore the lubricated chain itself gets contaminated by dust, glue and paper particles, preventing lubrication to reach the critical areas.
To prevent such problems lubrication can be minimized or completely shut off. But this can cause chain stiffness and uneven elongation of the chain strands, which may lead to production errors and early replacement of the chain. With Tsubaki Traypacker Chain, the internal lubrication cannot transmit to products, which eradicates contamination. Also the consistent internal lubrication combats the risks of uneven wear and elongation, and does away with the need to apply expensive food grade lubricants.
Significantly Tsubaki Traypacker Chain is slightly narrower than standard Lambda chain, a requirement for most tray packing machines. Further, the machines require pushers to be fitted to the transport chain and for this Tsubaki’s designers have developed a bespoke solution in which the attachments are mounted by an engineered extended pin that allows flexible spacing so that different packing configurations can be accommodated.
Additionally, Traypacker Chain is supplied with Tsubaki’s Match & Tag Service to guarantee a minimum length tolerance between chain strands that run parallel for conveyance purposes in for instance packaging machinery. Multiple case studies prove that even in the most demanding 24/7 production processes Tsubaki Traypacker Chain shows an absolute minimum in elongation making its performance unsurpassed and offering unrivalled benefits year by year.
About Tsubaki
Established in 1917, Tsubakimoto Chain Company is the world’s premier manufacturer of power transmission products with strong market positions in premium quality industrial drive & conveyor chains and associated power transmission components such as cam clutches, reducers & linear actuators. With a turnover exceeding $1,5 Billion US Dollars & 6,500 employees, the Tsubaki group includes 46 production locations and 63 group companies worldwide. Our production and sales networks are now more developed than ever.
Tsubakimoto Europe B.V. serves Power Transmission customers in the Pan-European market, Africa and the Middle East from European headquarters located in Dordrecht, the Netherlands, along with a local subsidiary based in Nottingham, serving the UK market & Ireland and from the office in Gilching, Germany customers in Germany, Austria and Switzerland are served.
Brenntag expands service portfolio by acquiring the pipeline and chemicals services segment of Greene’s Energy Group
AdministratorBrenntag, the global market leader in chemical distribution, has just announced it has completed the acquisition of the pipeline and chemicals services business segment of Greene’s Energy Group, LLC, a leading provider of integrated solutions for the Oil & Gas (O&G) industry in the USA, headquartered in Houston, Texas. The business is focused on pipeline cleaning and hydrostatic testing.
Markus Klähn, Member of the Management Board of Brenntag Group and CEO Brenntag North America: “The acquisition complements our existing product and service portfolio for the O&G business in the USA and supports our ability to comprehensively serve all segments of the industry.”
The acquired assets of the pipeline and chemicals services segment of Greene’s Energy Group, LLC, offers a full range of products and services for pipeline integrity management, new construction and maintenance support including several proprietary chemicals and large inventory of specialized equipment.
Anthony Gerace, Managing Director Mergers & Acquisitions at Brenntag Group: “The acquisition will expand our capabilities and service offering in this important segment and is a good opportunity for further consolidation of the still fragmented market of service providers to the O&G industry.”
The business unit generated sales of approximately 15.5 million USD in the financial year 2016.
About Brenntag:
Brenntag, the global market leader in chemical distribution, covers all major markets with its extensive product and service portfolio. Headquartered in Mülheim an der Ruhr, Germany, the company operates a global network with more than 530 locations in 74 countries. In 2015, the company, which has a global workforce of more than 14,000 employees, generated sales of EUR 10.3 billion (USD 11.5 billion). Brenntag connects chemical manufacturers and chemical users. The company supports its customers and suppliers with tailor-made distribution solutions for industrial and specialty chemicals. With over 10,000 products and a world-class supplier base, Brenntag offers one-stop-shop solutions to around 180,000 customers. This includes specific application technology, an extensive technical support and value-added services such as just-in-time delivery, product mixing, formulation, repackaging, inventory management and drum return handling. Long-standing experience and local excellence in the individual countries characterize the global market leader for chemical distribution
Roskill's Salt 2017 conference - Global Opportunities in a New Era for the Salt Supply Chain
AdministratorIn the first few weeks of 2017 there was significant growth in international salt trade, driven by de-icing markets and low shipping rates. Many of the new salt production projects due on stream by 2020 to supply the de-icing market will produce salt via solar recovery methods, letting nature take care of the expensive job of salt crystallisation for free. Solar salt production already accounts for an estimated 40% of salt production worldwide in 2017. Essam Madbouly of Cristal Global and AT Kordy of Egyptian Salt and Minerals (EMISAL) will be talking about new investments in solar salt production at a conference organised by Roskill, a leader in a leader in international metals and minerals research: Roskill's Salt 2017 conference takes place March 28 to 29 at the Renaissance hotel in Düsseldorf, Germany.
Historically, Germany served as a centre for European salt trade, and today this industry is still served worldwide by maritime dry bulk shipping. Denny Sabah of Maritime Strategies International will be giving his perspective on salt and dry bulk shipping market trends and outlook on the first day at the conference, in a session which will also include insights from Robert van Muiden of Rotterdam Bulk Logistics and Hugo du Mez of the Port of Rotterdam Authority.
Increased investment by salt producers in new sources of cost effective production will underpin growth in the chloralkali sector in Asia. Growth in salt consumption has been particularly strong in China, which is a net importer of salt despite its position as the largest salt producing country in the world. Competition within the salt industry, particularly over the lucrative and sporadic road de-icing market will continue to affect market shares. Patrick J. Laracy, President of potential new entrant to the market, Vulcan Minerals, will be describing at Salt 2017 how his company plans to take advantage of this market for salt. Per Nygaard, International Principal Manager for salt at Azelis, a leading de-icing salt distributor, will elaborate on how the de-icing salt supply chain works in Europe.
According to Roskill, world salt revenues have achieved a steady annual average growth rate to 2017, despite the slowdown in chloralkali markets in recent years. The strongest regional growth in the medium term will continue to be in Asia, but the more mature markets of NAFTA and Europe are also growing. At the conference Roskill will aim to put raw material, regulatory and technology developments within the salt industry into context. The 15th edition of Roskill's global salt report, Salt 2016 Global Industry Markets & Outlook, was published in late 2016
Roskill reviewed the production plans of more than 300 salt production assets worldwide during the research for its 2016 report. Germany's K+S has retained its position as the largest producer in the world, fending off a hostile takeover bid and announcing two major expansion projects during 2015/16. As the cost of shipping salt across oceans has fallen, traditional European salt producers are finding that they have to compete with new suppliers from as far away as Australia, Mexico and Chile. Wouter Lox of EuSalt - the European salt producers' association, will be speaking at the conference about the regulatory and legal challenges that European salt producers face in 2016. Vladimir Sedivy, the President of Salt Partners, a Swiss engineering consultancy, will present a paper in the same session on what drives the salt and chloralkali industry in Europe.
Chloralkali production is the largest end-use for salt. Chlorine is the raw material for the production of numerous organic chlorine compounds, the most important of which in terms of volume is ethylene dichloride, a chemical precursor to the 46Mtpy commodity polymer, PVC. Dr Jason Leadbitter of Inovyn Chlorvinyl will update delegates on Inovyn's sustainability programme for salt in PVC manufacture. Caustic soda also has a very wide range of end-uses including alumina manufacture, pulp and paper production, and chemical processing. Synthetic soda ash production is the next largest end-use for salt, and this in turn is mainly consumed in glass applications. Dr Henry Lau of Shihlien Chemical Industrial Jiangsu, a major Chinese soda ash producer, will be describing his company's new 300ktpy pharmaceutical grade salt facility at Salt 2017. Another major Asian chloralkali producer, Aditya Birla, will be putting forward an Indian perspective on chloralkali trends.
The USA remained by far the largest destination for salt shipments in 2016. Chile remained the main supplier to the USA in 2016, supplying an estimated 4.5Mt, mainly for road de-icing applications. Australian salt exports in 2016 were an estimated 8.5Mt, maintaining its longstanding position as the world's largest salt exporter. However, this total was down on exports in 2015. Australian producers export salt to Japan, China, South Korea and Indonesia for use in the chemicals industry. This decrease in salt shipments from Australia to Asia during 2016 was partly due to increased competition from Indian exports. Between 2010 and 2015, Indian salt exports to China increased from 0.4Mt to 2.3Mt, averaging 42% py growth. Dev Salt, a major Indian producer of solar salt, will be describing the current status of the Indian salt industry in 2017 at the conference and explaining how Indian producers have achieved such spectacular growth in exports.
Long distance trade is a critical topic for the salt industry and this conference brings together salt producers, specifiers, traders, end-users and equipment manufacturers from every continent. The Roskill conference provides an international forum to debate the current technical issues and market developments (www.roskill.com). As low shipping rates facilitate the movement of salt as never before, these industry players need a regular opportunity to meet and discuss business.